Screw Feed Worm
Screw feed worm
For DRI, HBI and steelmaking industries
Function
How It Works and operation
Screw feeders are critical components in the Direct Reduced Iron (DRI) production lines, Hot Briquetted Iron (HBI) processes, and steelmaking industries, transferring materials under harsh operating conditions. They are designed to withstand high temperatures and severe wear, specifically in environments where temperatures can reach up to 800°C. These feeders are responsible for feeding materials such as sponge iron into the production line, ensuring precise and efficient material flow while maintaining the integrity of the system. The advanced manufacturing techniques, including the use of tungsten carbide coatings and hard-facing through 7-axis robotic additive manufacturing, provide durability, wear resistance, and a consistent coating quality for prolonged operational life.
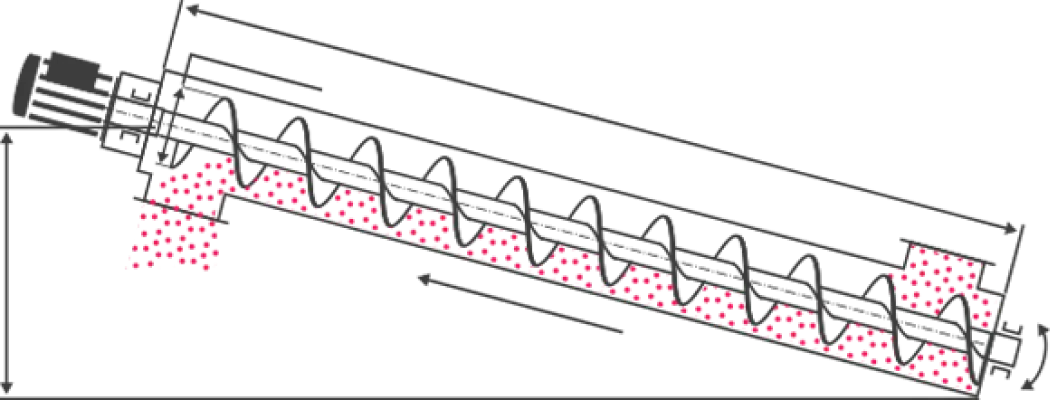
Specifications
Materials and Construction
The screw feeders are constructed using high-quality 310 stainless steel as the base material, chosen for its ability to withstand extreme temperatures and corrosion. The specialized coating is made of tungsten carbide alloys, providing superior hardness and wear resistance. The hardness of the coating ranges from 55-60 HRC, ensuring that the screw feeders can handle the demanding conditions of the steel industry. The hard-facing of all surrounding surfaces is performed using a 7-axis KUKA robot via additive manufacturing, ensuring precision, repeatability, and a uniform coating layer. These features help optimize the performance and longevity of the screw feeders, even in the most severe environments.
Product features
Design and Innovation
The design of the screw feeders incorporates advanced technology, including the use of 7-axis KUKA robotic systems for additive manufacturing. This process allows for precise hard-facing of the feeder surfaces, providing uniformity and durability. The use of tungsten carbide alloys as a coating material offers enhanced wear resistance and the ability to withstand high temperatures, ensuring that the feeders perform effectively in DRI production lines and HBI processes. TGT CIT’s proprietary method for laser cladding further enhances the mechanical properties of the screw feeders, providing a metallurgically bonded, low-dilution coating that significantly improves performance in harsh environments.
Competitive Advantages
Design and Innovation
TGT CIT’s screw feeders stand out due to their superior durability, wear resistance, and high-temperature performance. The composite coating, which includes more than 60% tungsten carbide, ensures an extended service life in comparison to similar products. Additionally, the precise hard-facing process, which is fully automated with high controllability, repeatability, and uniformity, results in an optimal quality product. This makes CIT’s screw feeders a cost-effective and reliable solution for industries requiring high-performance parts, especially when compared to traditional coating techniques. The advanced manufacturing methods also enable CIT to offer screw feeders that are more resistant to wear and corrosion, even in extremely harsh operating conditions.