Rotary equipment
Get to know Rotary equipment Group
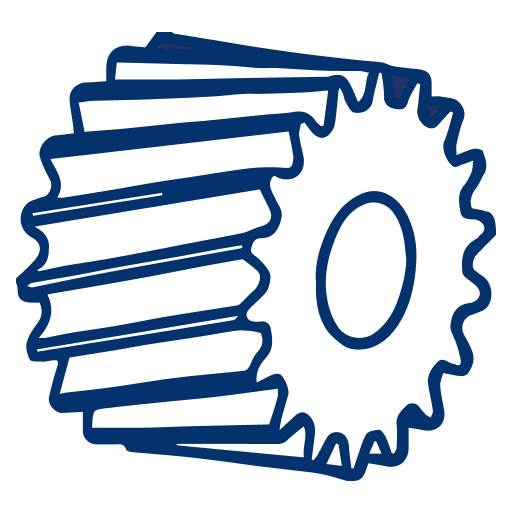
Which element in a rotary equipment?
Many industries possess vital equipment that runs by kinetic energy…
Which element in a rotary equipment?
Many industries possess vital equipment that runs by kinetic energy. Some examples are pumps, compressors and briquette rollers. Steel manufacturing complexes also possess huge rotary drums rotated by a pinion, these pinions are required to have wear and fatigue resistance. Overall, any element in a rotary equipment which requires an upgrade for its resistance capability can be coated by laser technology in TGT.
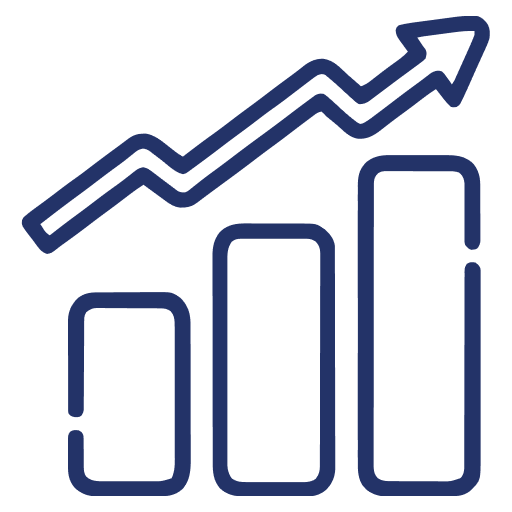
Importance of the overhaul and repair cost
Rotary devices are required to have annual overhaul or full repair …
Importance of the overhaul and repair cost
Rotary devices are required to have annual overhaul or full repair after few years. For this reason, having a durable and high-quality manufactured parts in a rotary device can be economically beneficial. Two of the main faults that can stop a rotary device is wear and fatigue during a long time in their parts. In order to prevent from this phenomenon, TGT company will offer a practical solution for solving the challenge such as laser cladding, chromium hardening and heat treatments techniques for enhancing durability of the equipment’s vital parts.
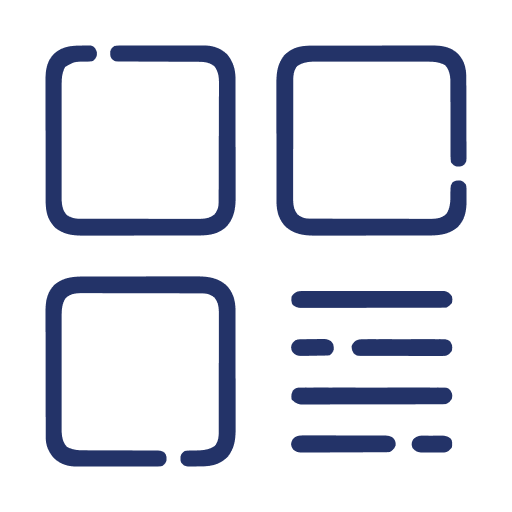
TGT offer for your application
TGT company possess one of the state-of-art laser technology system …
TGT offer for your application
TGT company possess one of the state-of-art laser technology system with the ability of welding, hardening and cladding. The specific method for material deposition is Direct Energy Deposition (DED) which has the minimum Heat Affected Zone (HAZ) among most of the material deposition methods. Other solutions such as face hardening and chromium layer depositing can be done in-house by TGT company for specific circumstances. By receiving an inquiry from our customers, we will analyze the fault and choose the right solution and materials for your challenge.
Explore and compare
Rotary Shaft
Rotary elements (shafts, axels and blades)
Most vital elements in a rotary device can be repaired or manufactured from scratch to keep the performance high. By using laser technology for depositing wear resistance materials. These rotary shafts can be repaired at its minimum delivery time and durability drop.
Coating Hardness:
55-65HRC
Minimum Distortion Down to
0.05mm
Total Run-out
Pinion
A crucial component for the optimal performance of grinding mills
Designed and manufactured according to AGAM standards using high-quality materials
Max Design Power
5 MW
Max. Gear Module
42 mm
Screw feed worm
recision Repair with Additive Manufacturing for Aircraft Single Crystal HPT Blades
Laser Directed Energy Deposition (DED) restores high-pressure turbine blades with precision, and enhanced thermal properties, offering superior control over complex geometries while preserving the blade’s crystal structure.
High-Temperature Resistance
up to
1500°C
Heat Affected Zone (HAZ)
down to
100 µm
5-Axis CNC Machining Tolerances
down to
0.02 mm
Turbine blades
Precision Repair with Additive Manufacturing for Aircraft Single Crystal HPT Blades
Laser Directed Energy Deposition (DED) restores high-pressure turbine blades with precision, minimal distortion, and enhanced thermal properties, offering superior control over complex geometries while preserving the blade’s crystal structure.
High-Temperature Resistance
up to
1500°C
Heat Affected Zone (HAZ)
down to
100 µm
5-Axis CNC Machining Tolerances
down to
0.02 mm
Why TGT is the best place for your rotary equipment
Fast response and delivery time
One of the main advantages of fully domestic production of TGT company's products is the accuracy and flaw less control over production line. With having a highly capable 6-axis KUKA robot, 2 and 3 kW IPG laser source and multiple business partners all the inquiries and price evaluations will be done as soon as possible.
Innovative optimized product and solutions
TGT Company, based on the indigenous knowledge developed within the company, has been able to develop specific process plans and laser cladding knowledges which as been patented and published in ISI journals.
On-call 24/7 support and service
In response to the critical needs of industries, TGT has established one of the largest industrial customer service center capable for supporting industries repair and maintenance calls.